Keysight Technologies use simulation-powered digital twin to increase ROI on capital expenditures
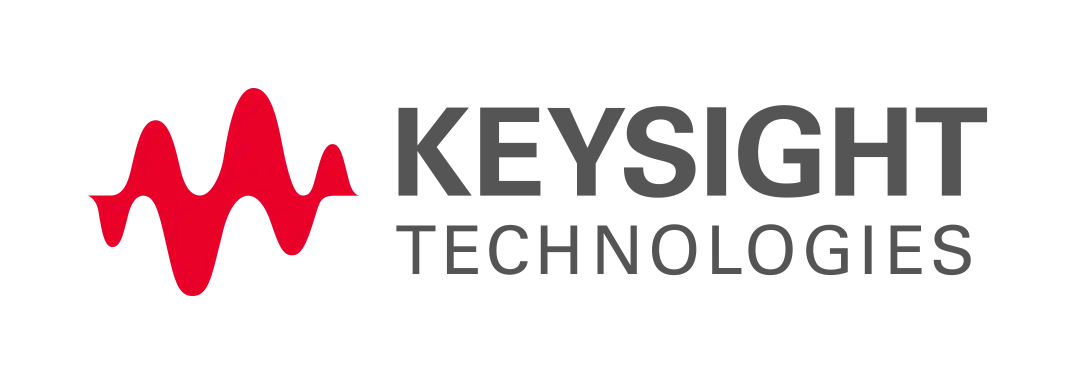
From saving millions in manufacturing costs, to transforming lives by improving healthcare delivery, we're proud of the success Simul8 users have achieved.
Ready to join them?
Johns Hopkins' emergency department process improvement with Simul8.
Norvik foods appointed Production Support 56 to help modernise production to diversify their product range and increase throughput.
Fiat Chrysler improved manufacturing throughput by 39 units and increased revenue by $1,000,000 per day at its Brampton plant.
Virginia DMV identified a staffing model to reduce customer waiting times to 20 minutes or less across 74 customer service centres.
UK Defense Equipment & Support used Simul8 to assess procurement options and model future demand to support the UK Armed Forces.
Changeology improved patient and staff experiences by using Simul8 to develop a bespoke method for scheduling appointments and optimizing resources.
Guy’s and St Thomas’ ACU uses simulation with the aim to increase capacity and reduce waiting times, thereby enhancing service quality and clinical outcomes.
NSPCC partnered with OR Society, AtkinsRéalis, and Simul8 to optimize helpline resource planning and improve response times for child welfare concerns.
Plexus guaranteed production capacity, identified optimum staffing levels, and saved $5,000 in equipment costs in just a few days.
Air Canada achieves a frictionless migration to a new system and enhances the contact center customer experience with a simulation-powered digital twin.
Controlant uses simulation to triple production of data loggers to monitor global Covid19 vaccine distribution.
NHS Isle of Wight utilized Simul8’s Bed.P.A.C. simulation tool to rapidly test a wide range of bed management scenarios to maximize efficiency and drive success.
Our partners at Production Support 56 were appointed by Allied Protek to help them validate their new plant design using Simul8.
London Health Sciences Centre projected $10 million of potential cost savings over span of 8 years using simulation.
Memorial Health System improved patient waiting times and ensured the feasibility of a $31 million capital investment project.
Louisiana Department of Health simulated post-storm patient air evacuations to hospitals in neighboring states, improving planning and saving 80+ hours of work.
FUJIFILM analyzed the return on investment of large-scale process changes and equipment that will enable output to be increased by 400% within five years.
FMC Technologies increased manufacturing throughput by 50%, removed bottlenecks and forecasted 5 year production to meet demand.
Geisinger Health System improved patient satisfaction by planning and implementing an on-demand, in-room meal delivery system using simulation.
Vidant Duplin Hospital identifies an approach to maintain left without treatment (LWOT) rates in the face of increasing ED patient volumes.
Gatwick Airport shortened the check-in process, reduced queue times and improved airline efficiency, without increasing investment.
Scarborough used Simul8’s simulation software to validate and implement improvement scenarios, delivering an annual cost savings of more than $50,000.
Developing smarter maintenance rules, GM increased manufacturing throughput by 5% and met an increase in demand.
South African charity Shout It Now's ground-breaking efforts improved HIV screening and treatment to save millions of lives.
HP saved $100,000 annually and achieved productivity gains by determining the most effective set-up for their process.
Simul8 was used to develop an integrative approach to optimize the manufacturing process design for NASA's Ares 1 launch vehicle.
Boston Scientific tested a range of process improvement scenarios to make production efficiency savings of $150,000.
RSI developed a tool to assess the public health system’s response in the event of a terrorist attack on the US food supply chain.
Logistics organization CHEP validated that investment in automated machinery would quickly provide a return to shareholders.
Motor carrier ABF Freight discovered the most efficient and economical approach for optimizing its dock operations.
Denver Police Department identified whether investment in additional equipment or staffing would improve lab turnaround times.
Applied Research Services Inc identifies the impact of prison policy and budgetary changes and saves $250 million of taxpayer money.
Indesit ensured the successful deployment of a new conveyor system by testing a range of control rules to identify the best solution.
Kelly Services evaluated ways to optimize business processes across the company's 1,400 branch and corporate offices.
NIBCO identified a new distribution strategy that reduced inventory by 40% and cut systems costs by 12%.
NHS 24, a critical service providing telephone healthcare advice, used Simul8 to develop a new staffing plan to cope with higher demand.
St Luke’s University Health Network avoids six figure cost by optimizing vaccine rollout with the help of simulation.
Explore the wealth of features that make Simul8 the #1 choice for simulation.
Learn more