Using a simulation-powered digital twin to streamline daily logistical operations and minimize disruption to the retail supply chain network
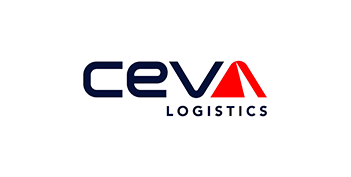
- Industry
- Logistics
- Location
- Brandenburg, Germany
- Goals
- Create a simulation-powered digital twin to reduce costs and improve resource allocation in the inbound area of a fashion retailer’s fulfillment center.
Achievements with Simul8
-
-
Digital Twin created to enhance routine operational planning
-
-
Average saving of 200 working hours per week
-
-
Increased fulfillment center weekly capacity by 2%
About the project
CEVA Logistics provides end-to-end supply chain management solutions to the automotive, retail, industrial, healthcare, technology, eCommerce, energy and aerospace sectors. The company specializes in freight management and contract logistics, with an annual revenue upwards of $16bn.
CEVA handles 125 retail logistics contracts in 25 countries and manages eight of the world’s top ten retailers' strategic supply chains. CEVA utilized Simul8’s digital twin technology to create a simulation-powered digital twin – a digital representation of their real-world process – to routinely improve resource allocation for one of its fashion retailer’s fulfillment centers and reduce annual operating costs.
What challenges did CEVA Logistics face?
Combined e-commerce sales in Western Europe (UK, Germany, France, Netherlands, Italy, and Spain) reached almost £330bn in 2022. Germany alone was responsible for an estimated 20% of all online retail trade in the same year. This surge in demand has increased the pressure on distributors to deliver fast and efficient customer experiences.
In this case, CEVA’s client needed to find a quick and cost-effective way to deal with the rapid throughput of large amounts of product in its Brandenburg fulfillment center.
However, the volatile nature of fast fashion created several challenges for logistics managers, including changeable levels of demand for stock, the need for swift and accurate turnaround times, and maintaining a tight hold on the fulfillment center's costs.
Furthermore, the complex nature of the fulfillment center’s operations made it hard to manually assess the daily, weekly, or annual impact of potential changes or improvements to the supply chain network. For example, experimenting in a real-world environment where the retailer needs orders to leave the center on time to meet demand could have significant consequences.
There was a need for the fulfillment center to identify the optimum number of employees required per shift to keep within a specified utilization percentage and avoid overburdening the system without disrupting operations. Using Simul8’s simulation-powered digital twin technology would enable planners to test new processes and implement changes to the supply chain network without impacting live activity.
"The project amplified the warehouse planners' processes, enabling them to allocate resources very precisely to the different stations. This allowed our customer to save working hours and invest in that free capacity in other areas and reduce costs.
We were also able to explore how the simulation reacts to extra volume, in order to further refine the process for the future."
Business Intelligence Specialist at CEVA Logistics
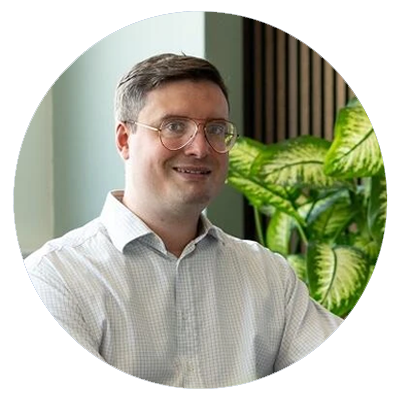
What did CEVA Logistics do to cope with the surge in demand?
CEVA worked with Simul8 to create a simulation-powered digital twin linked to real-time data from the fulfillment center’s systems. It began by working with the fulfillment center’s planners to understand their daily operations and Key Performance Indicators (KPIs), such as order processing time, throughput, resource utilization, and customer satisfaction. This advanced planning helped minimize the risk of high-volume volatility within the system and set clear parameters for the simulation.
When building the digital twin, there were three phases of the fulfillment center’s operations to consider including:
Inbound phase
Using metrics such as supplier direct receive and supplier direct putaway helped evaluate the efficiency of receiving goods directly from suppliers and accurately storing them in the facility. Similarly, intra-warehouse goods received and putaway KPIs assessed the effectiveness of internal goods transfers within the center. The returns received and putaway KPIs analyzed the handling of returned goods, ensuring streamlined processes and reduced processing time.
Storage space
Efficient storage management was critical to the day-to-day operations of the fulfillment center. Using a metric such as the rotation index helped logistics managers evaluate the efficiency of inventory rotation within the storage space. The simulation-driven digital twin captured valuable data on item turnover rates and storage utilization. Analyzing the rotation index allowed for the long-term optimization of storage configurations, picking strategies, and stock placement to maximize efficiency and minimize errors.
Outbound phase
The first KPI in the outbound stage was picking. By evaluating the accuracy and efficiency of the picking process, fulfillment center managers were able to optimize strategies, warehouse layout, and resource allocation to improve order fulfillment speed. Other KPIs in the outbound phase included: sorting, packing, vector sorting – sorting items based on shipping vectors or destination – and truck loading. Analyzing these processes allowed logistics managers to optimize sorting, packing, and loading procedures; improving outbound logistics and minimizing delays.
A regular digital twin will provide a static representation of a system's current state. However, by adding simulation technology, the digital twin was able to understand the dynamic behavior of the system, its process rules, and how each element interacts with others. This technology enabled CEVA to conduct continuous ‘what if’ analysis. It facilitated advanced optimization by running thousands of permutations to evaluate and then optimize the different strategies available. In this way, the simulation-powered digital twin could inform process owners on the best corrective action to take, whether responding to different inputs, potential challenges, or changes to the operating environment. Furthermore, the robust simulation engine enables the digital twin to adapt in real-time, meaning quick adjustments can be made based on emerging data to forecast future process performance.
Implementing simulation-powered digital twin technology offered granular insights into the fulfillment center’s dynamic operations, which minimized risk, reduced downtime, and accelerated time to market.
The Results
Following the creation of the simulation-powered digital twin, fulfillment center planners could allocate resources efficiently and determine the precise number of staff needed at each phase. The result was an average saving of 200 working hours per week and a 2% increase in capacity across the facility.
Furthermore, the digital twin publishes results hourly and delivers crucial data to the fulfillment center’s control room operators. This information contains analyses of actual inventory versus forecasted and simulated inventory.
These results enabled fulfillment center managers to optimize staffing levels within the facility on specific days and shifts. Not only did this improve utilization rates, but it also ensured the system was never under too much stress.
Using data visualization software, the control room operators were able to track KPIs relating to the inbound phase, storage space, and outbound phase on a daily basis. The data generated from this monitoring process was fed into the simulation to ensure the system made predictions based on real-world metrics.
Check out our free ebook
Why aren’t more businesses taking advantage of simulation-based digital twin software?
Get your ebookYour Simulation Maturity roadmap
Amplify decision-making using our whitepaper as a complete guide for Simulation Maturity readiness.
Download now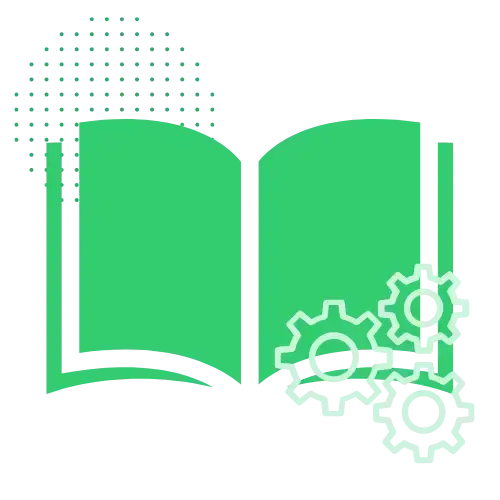