Using a simulation-powered digital twin to transform day-to-day decision-making in fast fashion logistics
Optimizing DHL’s largest distribution center in Latin America
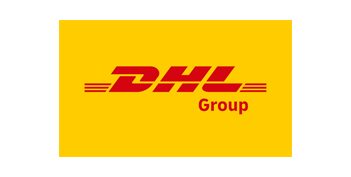
- Industry
- Logistics
- Location
- Louveira, São Paulo State, Brazil
- Goal
- Develop a simulation-powered digital twin for routine operational planning to streamline day-to-day warehouse picking efficiencies for one of Latin America’s largest distribution centers.
Achievements with Simul8
-
-
Digital twin for routine operational planning with 98% accuracy
-
-
Increased productivity and fewer issues due to lack of resources
-
-
Improved profit margins and customer satisfaction
About the project
DHL Group is the world’s leading logistics company, with over 600,000 people working in 220 countries and territories. It has transformed the logistics sector and delivers an estimated 1.7bn parcels annually, with its operations in the Americas generating over €22 billion in 2022 alone.
However, experts suggest global parcel shipping volume will reach 256 billion by 2027, and demand will continue to grow. Why? Consumer purchasing habits are constantly changing, and same-day or next-day delivery has become the norm. This has increased the pressure on the logistics sector to streamline its processes to offer seamless customer service.
As a result, using technology to inform order fulfillment strategies has become a priority for distributors. Increased efficiency and productivity can reduce warehouse costs, improve customer satisfaction, and make pickers’ jobs easier.
DHL recognized that using manual systems to forecast staff levels for its picking operations was limiting efficiency at its Louveira distribution center in São Paulo State, Brazil, as well as causing issues with customer relationship management. The logistics giant approached Simul8 channel partner in Brazil, Simulate, to develop a simulation-powered digital twin for routine operational planning that could help address the complex issues within its warehouse processes and identify ways to continuously optimize picking staff resources on a regular basis.
What challenges did DHL face?
Time is a constant pressure in a distribution center. The dynamic nature of incoming orders makes predicting and allocating resources difficult, so hitting daily picking targets to ensure customers receive their goods on time can be problematic.
Furthermore, e-commerce trends such as fast fashion mean that there is a quick turnover of styles and frequent product launches, which places heightened pressure on distribution centers to process and dispatch orders promptly. For example, McKinsey found that 23% of customers were willing to pay a premium for same-day delivery, necessitating the need for an agile and responsive fulfillment strategy to keep pace with the accelerated product lifecycle.
The challenge for DHL’s Louveira distribution center was to create the optimal allocation of resources to ensure it could meet demand and hit daily targets. It required a simulation-powered digital twin that could be used routinely to adjust resourcing levels as needed within a constantly changing environment.
The center handles more than 5,000 product SKUs, and logistics managers were previously reliant on Excel spreadsheets to allocate the correct number of pickers needed for each shift. When forecasting the number of workers required, shift managers had to consider the level of demand each day and the complex touchpoints within the picking process, such as the time it takes to locate an item, the size of the package, and if it’s easy to access or requires the use of a forklift.
For example, for the first twenty days of the month, the number of parcels picked remains consistent, but in the final ten days of the month, order numbers surge, and more pickers are needed. So, if there aren’t enough pickers on shift and it becomes clear targets will not be met, DHL has to contact its clients and inform them they will not receive their goods that day. This led to fractious relations with customers and the potential for reputational damage – DHL could offer no guarantee that customers would receive their goods on time. It also increased the pressure on DHL’s workforce and supply chain network as staff rushed to complete orders, leading to inaccuracies in the picking process.
How did DHL manage these challenges?
Warehouse managers identified that using daily digital processes and, in particular, a simulation-powered digital twin to forecast the number of pickers needed for each shift would enable them to work out exactly how to meet demand and improve customer experience. Furthermore, creating a digital twin for routine operational planning would futureproof the process, enabling management to predict staffing requirements on a weekly, monthly, and annual basis.
Simulate delivered an in-house training course to a specialist team that DHL had assigned to lead the project. Utilizing Simul8’s technology and expertise in the logistics sector, the simulation team created a simulation-powered digital twin of DHL’s warehouse management system and a simulation nicknamed the ‘Crystal Ball’ because it predicted staffing numbers for each shift.
The simulation-powered digital twin of the warehouse management system was used to understand the day-to-day operations within the center, such as the daily throughput of orders, how long it takes to process those orders, and which shifts are the busiest and require extra pickers to cope with increased demand.
Subsequently, the real-time data extrapolated from the warehouse management simulation was inputted into the Crystal Ball to generate accurate estimates of the number of staff required for each shift. Having the crystal ball simulation working in tandem with the simulation-powered digital twin improved the day-to-day efficiency of warehouse processes and continuously reduced resourcing issues.
The process took almost five months to complete and included developing several conceptual simulations to ensure the final specification delivered the level of accuracy the team required. It was a complex project, as all 5,000 product SKUs had to be mapped into the simulation and constraints such as time of day, month, or year also had to be considered. However, once completed, the team had access to a digital twin for routine operational planning that could be used infinitely and scale with the center’s operations. The benefit of conceptual simulations meant the team could test real-world scenarios in a hypothetical environment, which informed future decision-making processes.
Check out our free ebook
Why aren’t more businesses taking advantage of simulation-based digital twin software?
Get your ebookYour Simulation Maturity roadmap
Amplify decision-making using our whitepaper as a complete guide for Simulation Maturity readiness.
Download now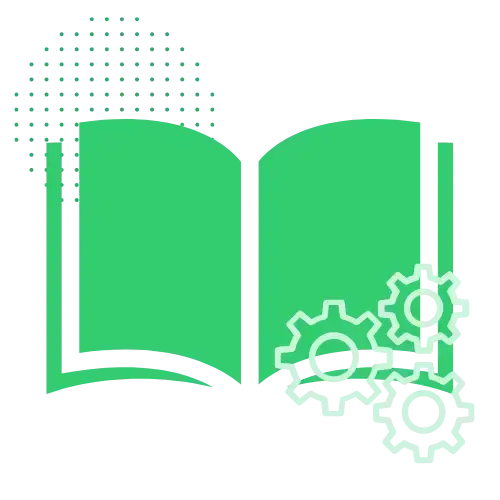