Indesit identifies optimum deployment of a new conveyor system
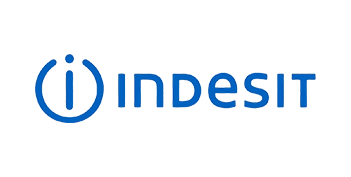
- Industry
- Manufacturing
- Location
- Fabriano, Italy
- Project goals
- Design and test control rules for new conveyor system
Achievements with Simul8
-
-
Increased understanding of the whole system
-
-
Confidence that the solution would work prior to installation
-
-
New system can better manage the complex product mix more effectively
The challenge
Indesit Company is one of the European leading manufacturers and distributors of major domestic appliances (washing machines, dryers, dishwashers, fridges, freezers, cookers, hoods, ovens and hobs). It is the undisputed leader in major markets such as Italy, the UK and Russia.
The existing production line at a Cooker manufacturing facility relied on human product allocation from 8 assembly lines into a 14 lane sortation area. Due to the complicated product mix in the factory, it proved very difficult for a human to assess which item should go to which lane and change lane allocations in a quick and accurate manner.
Getting the lane allocation wrong or not changing it in time for new models easily caused a bottleneck, possible production losses and extra work for the distribution department.
To maximize the efficiency of the process a PLC conveyor system that automatically allocated a range of unique products to sortation tracks at the end of these assembly lines was to be installed. Simul8 was used to design and test the control rules of the system before installation.
"We chose Simul8 because it provides rapid model development, a high degree of control over entities within the simulation and superior graphical execution of the model that helps with troubleshooting and customer buy-in."
Systems Engineer, Indesit
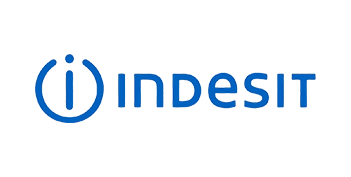
The solution
Martyn Hogg, Systems Engineer at Indesit, used Simul8 simulation software to simulate the system in conjunction with a specific tool for tracking product types.
The simulation was configured to run on actual data collected from barcode scanners in the factory production lines. This enabled a validation exercise to take place, giving conclusive evidence that the simulation was behaving as the system would do under general working conditions.
After this, it was possible to experiment with a series of different control rules to find the best automated allocation system before this was implemented in the real factory.
Martyn developed a Visual Basic program to communicate with Simul8 and the existing Lane Allocation Software simultaneously. In the simulation, when a product arrives at the sortation system, Simul8 sends a COM message to the Visual Basic program.
Then, when a product arrives at a lane, Simul8 checks if the model matches the model allocated to that lane. If they match another COM message is sent, representing the lane delivery signal that is sent in the factory.
The lane allocation data is sent to Simul8 to use to control the routing logic for the lanes. Simul8 sends lane delivery data when a product is delivered to a lane and also barcode information when a product arrives at the Sortation system.
The simulation allows quick and easy testing of different rules options. The simulation was used to test a wide range of control rules in order to find the one that best optimized performance so that this could be used in the real factories.
An example of one lane allocation rule is where a model is only allocated a lane if more than four units of that model are available for sortation. This leads to the build-up of models at this point in the process until each of these units are available.
The result
Simul8 was used to find the optimal set of PLC control rules to be implemented in the factory for improved throughput and efficiency.
As the simulation worked with actual production data it was able to provide results with an added level of accuracy.
Once the selection of possible rule sets had been tested, Simul8 proved which setup performed best and used its output data dynamically through the Lane Allocation software to dictate routing decisions though barcodes within the real factory.
The visual nature of the simulation allowed the solution proposals to be easily communicated to company management to get buy-in. The simulation was also used to train personnel in sortation and distribution procedures. Simul8 software is still being used regularly within Indesit Company to test assembly line and manufacturing "what-if" scenarios like this one.
Practical benefits of using Simul8 software for this work include:
- The new system can better manage the complex product mix more effectively
- Increased understanding of the whole system was realized through use of the simulation
- Simul8 provided confidence that the solution would work prior to installation
- The COM functionality of Simul8 enabled it to be easily linked to Visual Basic to simulate communications between different equipment within the factory
Learn more about Simul8 for manufacturing process improvement
Find out more about how simulation is used by manufacturing organizations, read more case studies and access a range of learning resources.
Learn more