Discrete event simulation
A simulation is a computer model that mimics the operation of a business system, such as the running of a factory assembly line, the staff assignment of a hospital or call center, or the day-to-day operation of a bank.
How does discrete event simulation work?
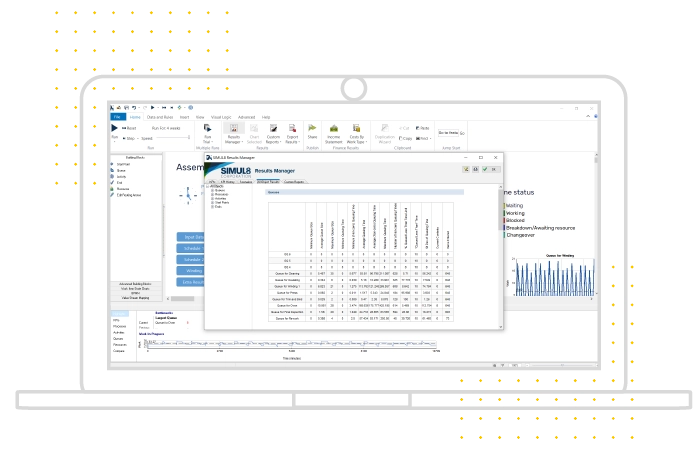
Discrete event simulation is a powerful technique for optimizing processes and making confident, impactful decisions.
Using intuitive discrete event simulation software like Simul8, you can build a visual mock-up of your process, similar to creating a flowchart. By adding timings and rules around the tasks, resources and constraints that make up your system, the simulation can accurately represent your real process.
Simulation offers a powerful, evidence-based approach to decision making - by using a virtual representation to test the impact of process changes and 'what-if' scenarios, you can find an approach that delivers the best results.
Key features of discrete event simulation
Time-based
Discrete event simulation is time based, and takes into account all the resources and constraints involved, as well as the way these things interact with each other as time passes.
This enables you to rapidly evaluate the long-term consequences of any changes and decisions you make.
Matches reality
It doesn't always take exactly 5 minutes for a customer to be served and a customer doesn't always arrive every 15 minutes.
Simulation builds in the randomness you would see in real life. So when you make changes to the simulation you see exactly how the system would behave in real life.
Effective testing
With discrete event simulation software you can quickly try out your ideas at a fraction of the cost of trying them in the real world.
And, because you can try ideas quickly, you can have many more ideas, and gain many more insights, into how to run your organization more effectively.
What can be simulated?
There are many scenarios that can be simulated. As a general rule, any system that involves a process flow with events can be simulated – so any process you can draw a flowchart of, you can simulate.
The processes you'll gain most benefit from simulating are those that involve change over time, variability and randomness.
For example, at a gas station nobody can guess exactly which time the next car will arrive, whether that customer will decide to purchase gas only, or how long they’ll take to make a purchase. Modeling complex dynamic systems like this effectively by any other method isn't possible.
Why use discrete event simulation?
There are many process improvements you can make using discrete event simulation software. For example, higher quality and efficiency from capital assets, better management of inventory, higher return on assets. But some of these improvements could be made without simulation.
So the real question is 'Why use simulation instead of another method?'
Discrete Event Simulation vs. Real Life Experimentation
Cost
Experimenting in the real world is costly. It is not only the capital expenditure of hiring new staff or purchasing new equipment it is the cost of the ramifications of these decisions.
What if you fire 3 staff and then find you can't cope with the workload and you lose customers? The only cost with simulation is the software and the man hours to build the simulation. Many of our customers have seen ROI of millions of dollars.
Repeatability
In real life it is really difficult to repeat the exact circumstances again so you only get 1 chance to collect the results and you can't test different ideas under the exact same circumstances.
So how do you know which idea is really the best. With simulation software you can test the same system again and again with different inputs.
Time
If you want to know whether hiring another 3 doctors will reduce patient waiting lists over the next 2 years you'll actually have to wait 2 years.
With simulation you can run 2, 10 or even 100 years into the future in seconds. So you get the answer now instead of when it is too late to do anything about it.
Discrete Event Simulation vs. Other Techniques
Interaction of random events
Some other mathematical tools can manage to effectively model a steady state scenario but only simulation lets you build in random occurrences like a machine breaking down and see the effects of this further down the line.
The more complex the scenario is the more these tools fall down and simulation software is the only answer.
Non standard distributions
Most other techniques force you to describe a situation approximately, "it takes an average of 5 minutes to serve each customer". In real life this isn't the case. It takes 3 minutes to serve the customer if they have 4 items, it takes 7 minutes if they have 20 items.
Approximating means results like staff utilization time and customer waiting times are all inaccurate. Only simulation gives you the flexibility to describe events and timings as they actually are in real life.
Makes you think
Simulation gets you thinking about all aspects of a process. The rule and data collection forces you to consider why elements work in a certain way, if they could work better. It brings to the surface inconsistencies and inefficiencies especially between different parts of a process who work independently.
Sometimes the simulation doesn't even have to be finished, the thinking it's made you do reveals the solution.
Communication
Simulation software is visual and animated, it lets you clearly describe your proposal to others. It's more convincing than just displaying the end results as people can't see where these came from.
Simulation is so effective at communicating ideas that many companies now use it as a sales tool to sell their products.
Find out how these organizations used Simul8 to transform decision-making
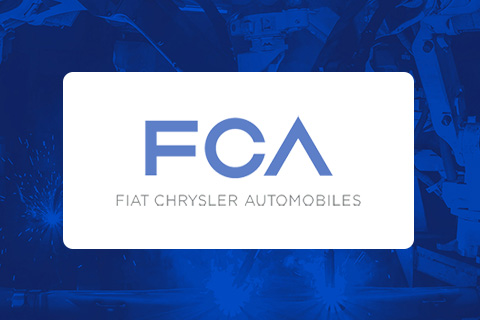
Meeting increased demand without additional costs
Fiat Chrysler improved manufacturing throughput by 39 units and increased revenue by $1,000,000 per day at its Brampton plant.
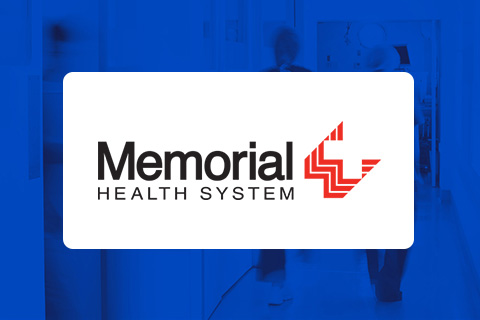
Ensuring the feasibility of investment and expansion
Memorial Health System improved patient waiting times and ensured the feasibility of a $31 million capital investment project.

Optimizing staffing to reduce customer wait times
Virginia DMV identified a staffing model to reduce customer waiting times to 20 minutes or less across 74 customer service centres.
Learn more about Simul8
Explore the wealth of features that make Simul8 the #1 choice for simulation.
Learn more