A Brief History of Simulation
Simulation has evolved from vast reconstruction projects to cutting edge AI-based technologies. This article takes you through the history of modelling and simulation - from early beginnings, to today's ever-innovating world where simulation is key for making day to day decisions and developing future strategy.
The background of simulation
The Great Mississippi Flood of 1927 was the most destructive river flood in the history of the USA. It flooded seven states, half a million people were displaced from their homes, and it cost the USA a third of its entire federal budget.
In an attempt to prevent future floods, the government decided to build the world's longest system of levees and floodways. However, these levees only targeted single sites - when a levee was built, that area wouldn't flood, but a town a few miles down the river would be completely destroyed. They needed to find a solution where they would be able to review the river system in its entirety in order to understand the interconnected relationships of the various floodways. At 2,00 miles long, however, this called for some real ingenuity.
In 1941, the visionary Eugene Reybold, director of the United States Army Corps of Engineers, had an idea. By building a large-scale hydraulic model, his engineers would be able to simulate weather and flood conditions to evaluate the effect of flood control measures on the entire system, not just one specific area, before then making improvements to the real-life system.
The Mississippi River Basin Model
Over the next 25 years, they set about bringing the idea to life. The Mississippi River Basin Model grew to cover 200 acres and was made of individual concrete panels contoured to match the real life land shape and river bed. It included tributaries, cliffs, lakes, flood plains, bridges and levees. Once built, an entire day of river flow along the whole system could be simulated in just five minutes. The team could then identify all weak spots and visit the equivalent real-life location to make the necessary improvements. It was an engineering feat of brilliance, the scale of which had never been seen before.
The Mississippi River Basin Model was a turning point in flood control management. Its greatest triumph came in 1952 when the information it provided prevented a huge flood in Omada and avoided as much as $65 million in flood damages.

It was also an early demonstration of how simulation could transform the way that important planning decisions are made, removing the real-life cost of trial and error, and ultimately save money.
An early attempt at lean manufacturing
This idea, of creating a model to replicate real life operations in order to analyse their effectiveness, was also later adopted by the research team at British Leyland.
In an attempt to better understand the throughput of its production line, in 1978 the team decided to create a small plywood model of the site so that they could analyse the movement of goods - represented by coins - through the production system. The goal was simple - to work out the most efficient way of managing production and throughput. What seems like a very simple idea today - building a rudimentary model of the system - was revolutionary at the time. They had simply not been able to see and review all aspects of the production facility in its entirety until it was mapped out in a simple model. From here, operations could be reconfigured to reduce wastage and increase efficiency, ideas that would later be formalised in the lean manufacturing models that first came to prominence in the late 1980s.
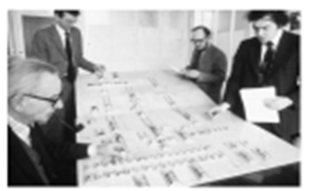
Unlike the Mississippi model, the British Leyland model aimed for small-scale simplicity. Most importantly, it was created to be flexible enough for the research team to reconfigure, test, and reconfigure again, and so became the world’s first visual interactive simulation tool.
Throughout the history of simulation, we have innovated - from the vast reconstructions of Mississippi or small plywood models at British Leyland, to becoming a digitised process that feeds into key decision-making right across industries. From predicting the number of ICU beds needed to cope with the Covid-19 outbreak, to routing your call when you phone a customer contact center, or reconfiguring a production line to meet new targets for throughput, digital simulation will most likely be working away behind the scenes as management teams seek out the most effective solutions with minimal disruption, or the cost of trial and error.
What is digital simulation?
A digital simulation is a computer model that completely replicates a real life process. By doing this digitally, rather than as a traditional flow chart, or on a spreadsheet, or with a model like those mentioned above, suddenly there is a far greater capacity to build complex processes where a multitude of conditions might affect outcomes. This enables a level of randomness that is more reflective of how things can be expected to behave under real world conditions, such as variations in demand surges or the need to deploy resources to respond to emergencies.
Once the model has been created to accurately replicate a real-life process, you then have a sandbox in which to tinker and test any changes to that process. Running the simulation under different scenarios then creates a wealth of insights and data to determine the best course of action before anything has been done to the real world process.
Suddenly decision making no longer needs to rely solely on forecasts based on past data, experience or hunches, but instead can look into the future with full understanding of the implications of each possible scenario.
What are the benefits of simulation?
For example, imagine that an airport has a problem with long passenger queues through security. A simulation can be built to model all the standard process behaviours and constraints involved in the passenger journey through the airport; typical passenger volumes arriving at the airport, the number of flights, the number of check-in desks, the number of security scanners, available departure gates, and how many employees are on shift.
Then take into account that some people will arrive two hours before they need to, while others arrive 30 minutes ahead of time. A few might even arrive with only minutes to spare. Some passengers will want to shop, others will want to eat or grab a drink in the airport lounges. Someone will lose their passport. A large group of passengers will hold everything up as they try to organise themselves. Perhaps several staff fall ill on the same day, or maybe bad weather has caused a number of incoming flights to be severely delayed. Perhaps a scanner breaks down and there is an hour where it is out of action...
Planning for all of this by referring to averages based on past data is possible, but the margin of error will increase with every contingency. Drawing a flowchart will only get you so far. Digital simulation, however, has moved this planning capability on significantly, opening the door to account for numerous layers of complexities and ‘what if’ scenarios. By modelling all possible outcomes rather than experimenting in real life with different scenarios and then waiting weeks or months to see the outcomes, organisations can fast track their decision to best case scenario with solid, evidence-based data built on a digital replica of real life.
Simulation allows organisations to rapidly pinpoint and test valuable opportunities for improvement - without any of the risk, time and cost of testing in a real-world environment - and then hit the ground running with the implementation.
Through this technology, it is now possible to design and then optimise a new process before implementation of the real system. It is possible to assess the validity and return of capital investment before investing any time and money. For a system that is already in place, it is possible to identify bottlenecks and experiment with changes to resolve them.
The future of simulation
Simulation has come a long way in the space of 70 years, and the future looks even more exciting. With the expansion of AI, Machine Learning, and the advent of IoT and Digital Twins, the future possibilities seem endless.
The widespread adoption of digital simulation can serve businesses of all scales in so far as it affords much more evidence for decision making. In effect, utilising predictive software provides a crystal ball of data. From day-to-day decisions to strategic digital transformation, fast, intuitive simulation software enables organisations to step-change their process efficiency and productivity, whatever their priorities and ambitions.
How can I get started with simulation?
Before Simul8, simulation software was costly, resource-hungry and time-intensive. We’re enabling everybody everywhere to make the right decisions with powerful and accessible software.
Learn more about Simul8